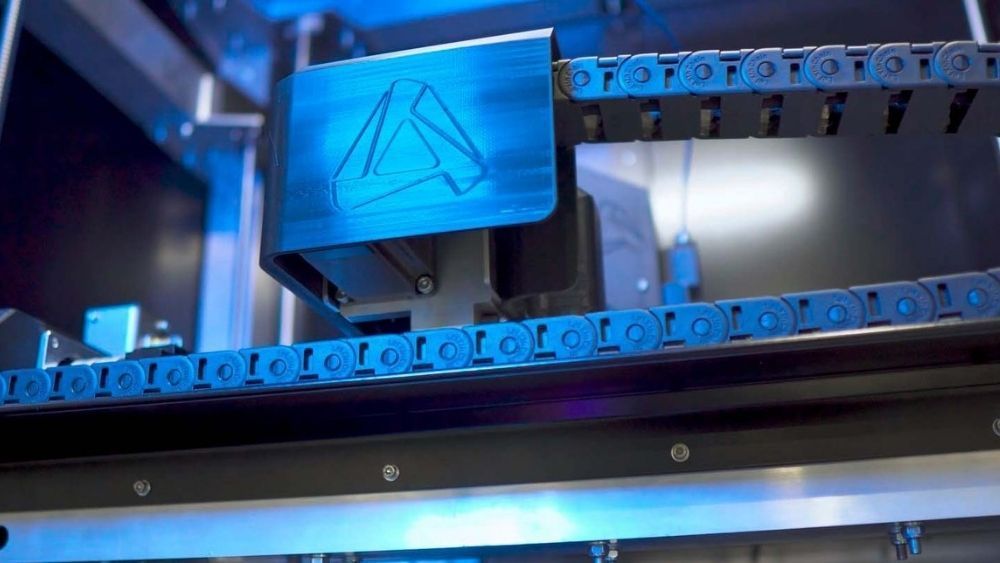
Being sustainable in every production process is trendy nowadays. Reducing the use of resources, the toxic materials production, waste and emissions is key to minimizing the environmental impact of the industry. Therefore, one of the pillars of the so-called industry 4.0 is additive manufacturing, and, stepping further, automated additive manufacturing.
Automated additive manufacturing is within the guidelines of the Sustainable Development Goals (SDGs) of the 2030 Agenda. It is specially aligned with numbers 9 (industry, innovation and infrastructure) and 12 (responsible production and consumption). Triditive, a pioneering startup in automated additive manufacturing in Spain, is committed to responsible production, on demand, avoiding excess and waste.
Sustainability: a ‘must have’ in additive manufacturing
In the words of Mariel, CEO of Triditive: “sustainability must be a default in the world we live, or, at least, it needs to be as present as possible”. It is clear that one of the differential values of additive manufacturing is precisely sustainability.
Use of strictly necessary material
Compared to subtractive manufacturing processes, waste is reduced in additive manufacturing. Only the material that will be part of the component is used. The production of a component concentrates on less material waste, energy use and machine emissions. Therefore, the environmental impact of additive manufacturing is lower than other production methods.
Prototype before producing
In addition to avoiding waste generation, by using the necessary material for each component, Automated Additive Manufacturing allows the making of prototypes in order to detect errors or optimize the design before producing the project. As a result, produced pieces match the final version. They are ready to use. This possibility saves time, money and resources.
Recyclable materials
Triditive works with metal, polymers and compounds. The commitment to using raw materials obtained from natural and renewable resources, as opposed to oil, is increasingly notable. In addition, users demand parts that can be recycled or reused, and that have a lower carbon footprint.
Automating additive manufacturing: lower environmental impact
Different from other methods, Additive manufacturing obtains the parts from the addition of the material. This technology reduces intermediate processes, allowing parts to be obtained up to 10 times faster. By betting on this production method, companies increase autonomy, reduce their production costs and commit to sustainability.
The future of additive manufacturing lies in its automation. Thanks to the use of software, industries are more independent. They stop depending on the supply chain and distant manufacturers, leaning towards local production.
According to the 2020 Advance of Greenhouse Gas Emissions by the Ministry for the Ecological Transition and the Demographic Challenge, 17.6% of GHG emissions are linked to transport. The commitment to local production reduces emissions, further gaining sustainability.
The solution for the supply crisis: additive manufacturing
Out-of-stocks in the supply chain cause losses of up to 4,000 million euros each year in Europe. Since the end of 2020, the global crisis in raw materials and industrial components has hit different sectors, causing bottlenecks and increasing prices. According to the latest quarterly report from the Bank of Spain, 22% of Spanish manufacturing companies have been affected by supply shortages.
However, through Automated Additive Manufacturing, Industry 4.0 has the potential to solve global supply problem. Triditive **provides a solution to digitize production processes, ease additive manufacturing and the supply of critical components: cloud automation software, EVAM**.
This cloud automation software is an essential innovation that has been awarded GoHub’s “The Global Water Challenge”. Environmental impact of additive manufacturing is significantly lower than that of other production processes, its automation through software unites design and production, avoiding, even more, waste and intermediate processes.