Once we have created our projects, with their assemblies, sub-assemblies, parts and components, it is time to convert them into a tangible product, so we make use of the production orders, the orders can be made up of complete projects, part of them or pieces of different projects. The minimum unit of an order is the JOB, these units, depending on the production technology can be grouped into BUILDS, to maximize the volume of printing, materials and optimize delivery times of orders.
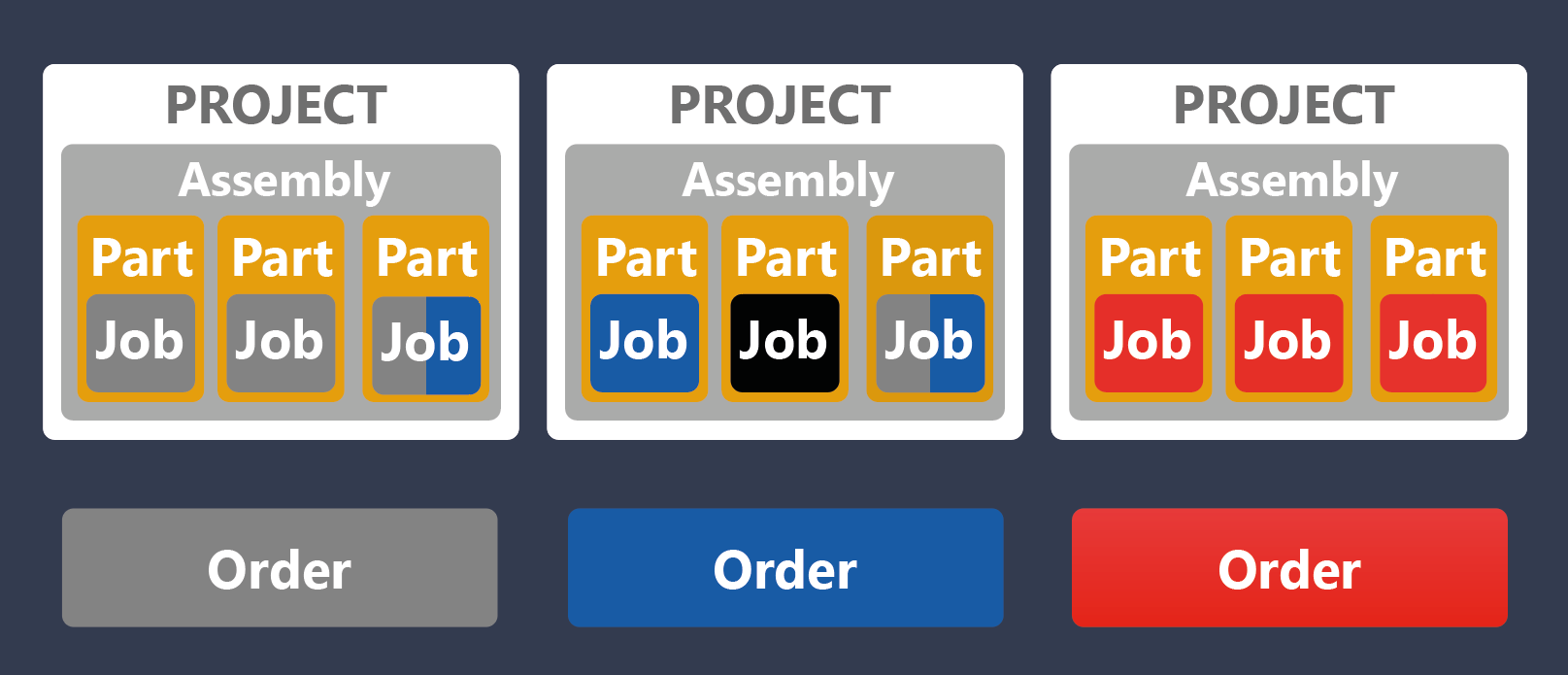
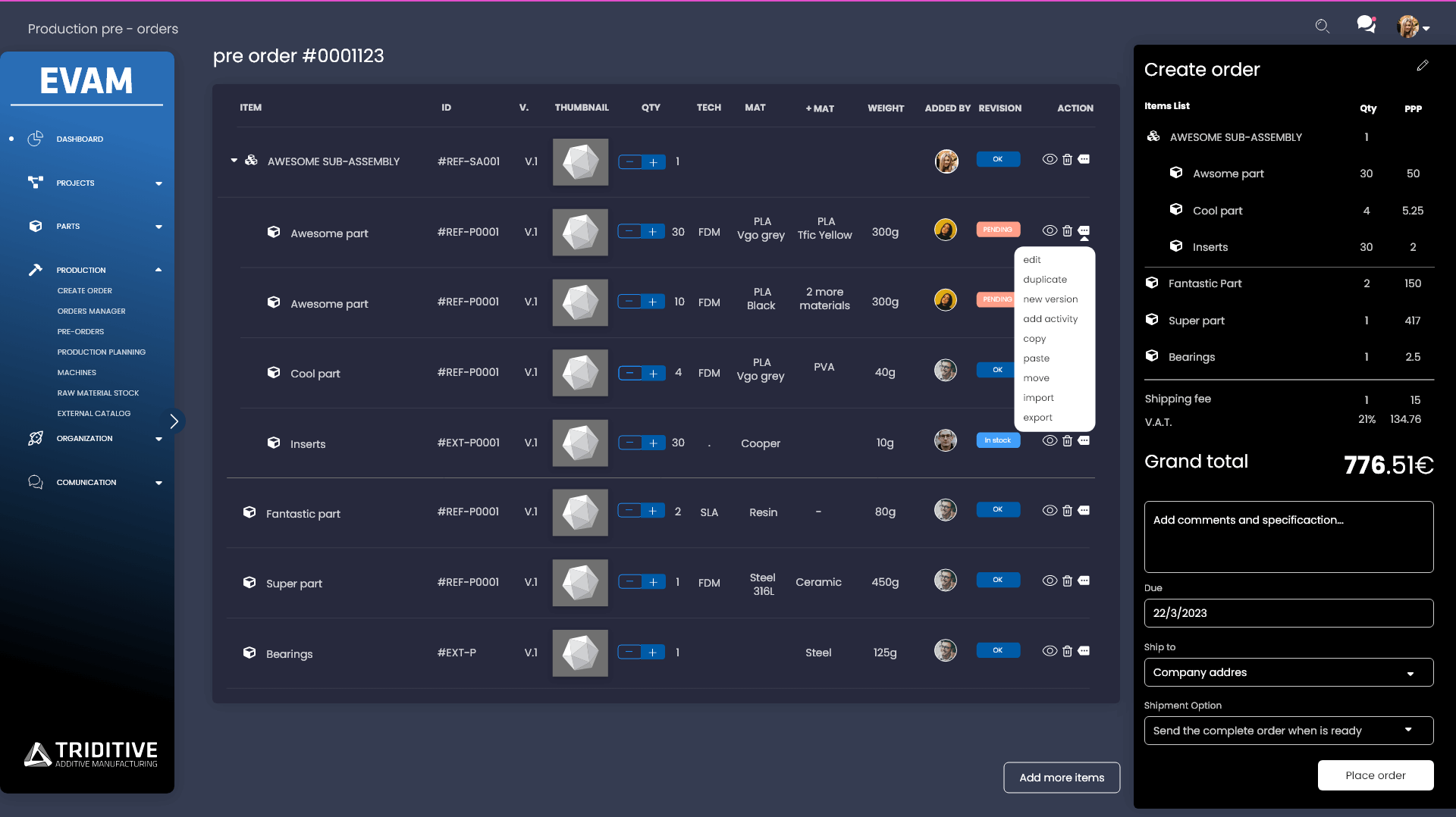
We can create pre-orders, in this way we will preview the cost that will have, these pre-orders are made by the users, average costumer, and advanced costumer, At this point we can add the desired quantity and colors of each of the components. Once these orders have been analyzed, the product Ingeneer converts it into an ORDER by prioritizing production times or customer requests.
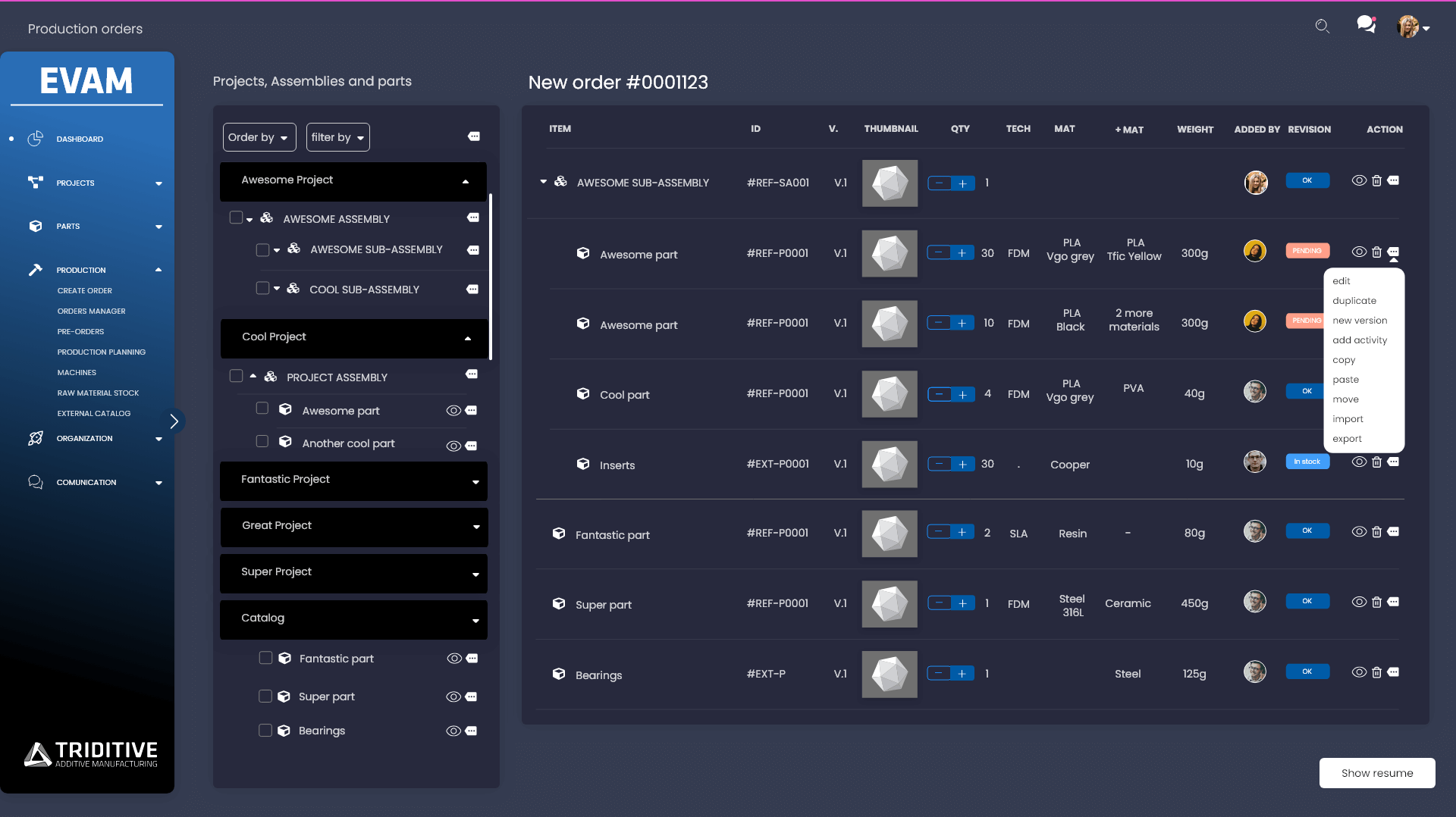
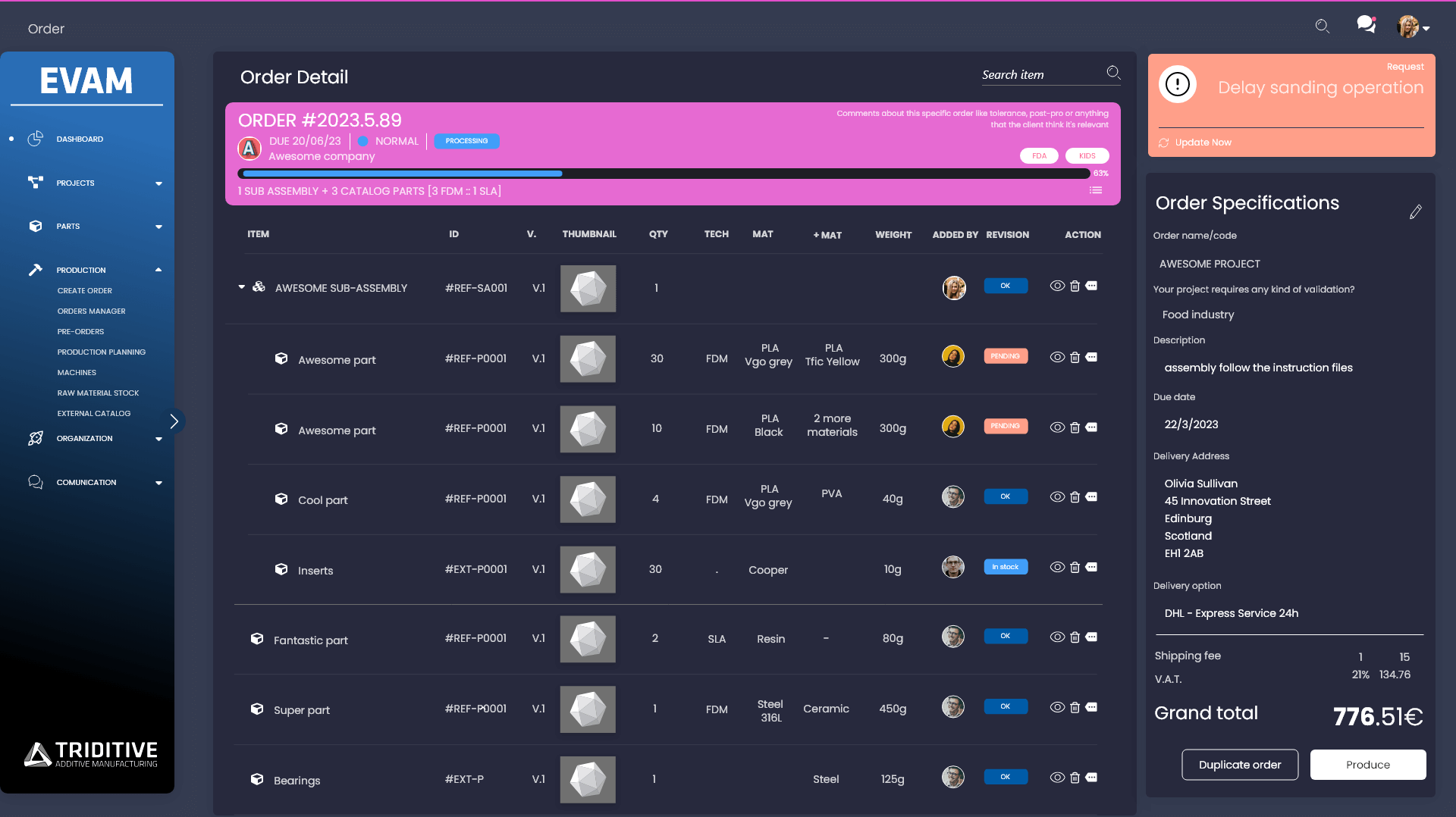
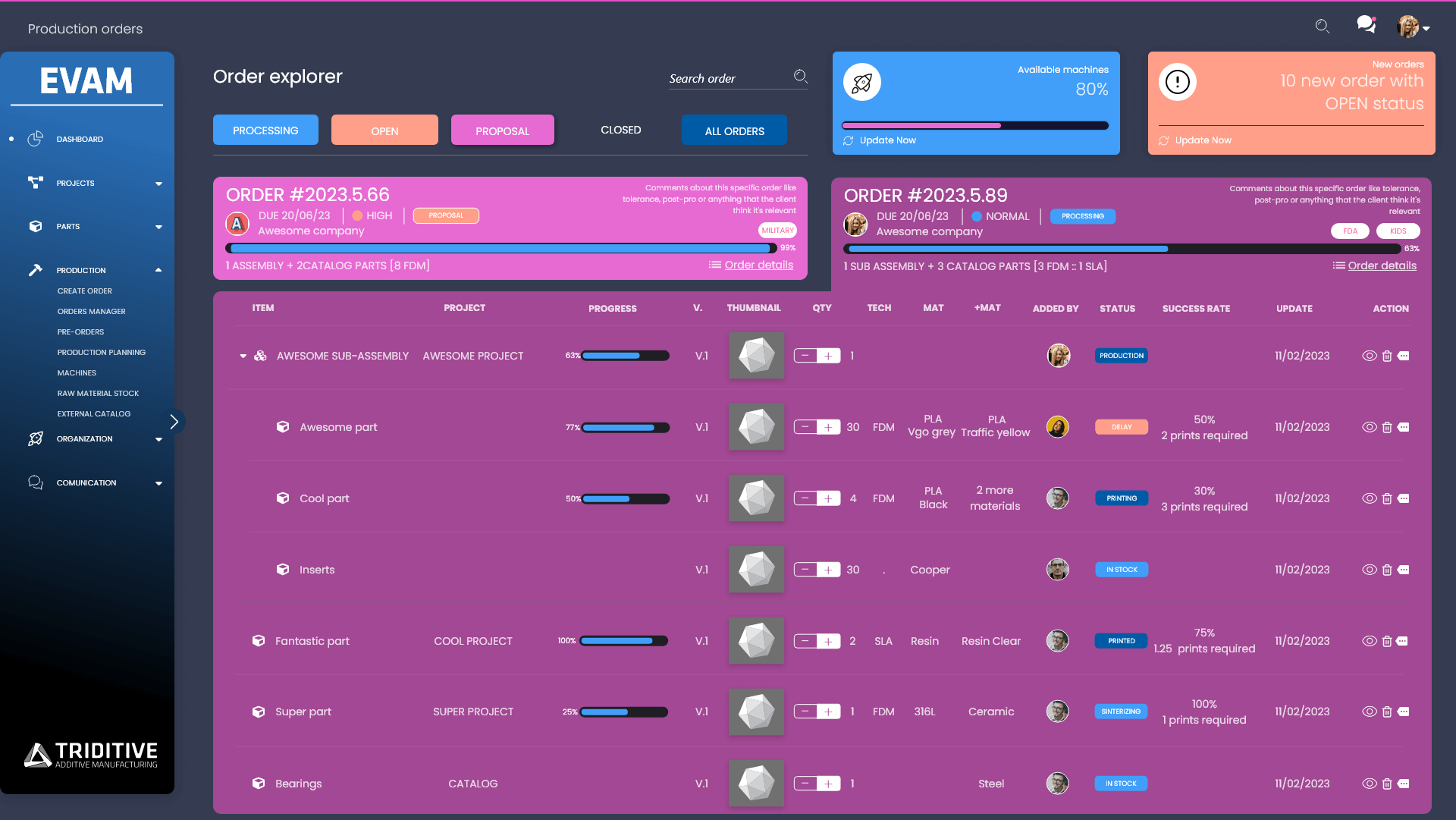
Once the preorders pass to order status they are transferred to the production manager user, who manages the resources to carry them out, executes the necessary actions on the files such as gcode file conversion or build creation and according to the assigned priority and the availability of resources schedules the manufacturing and post-processing.
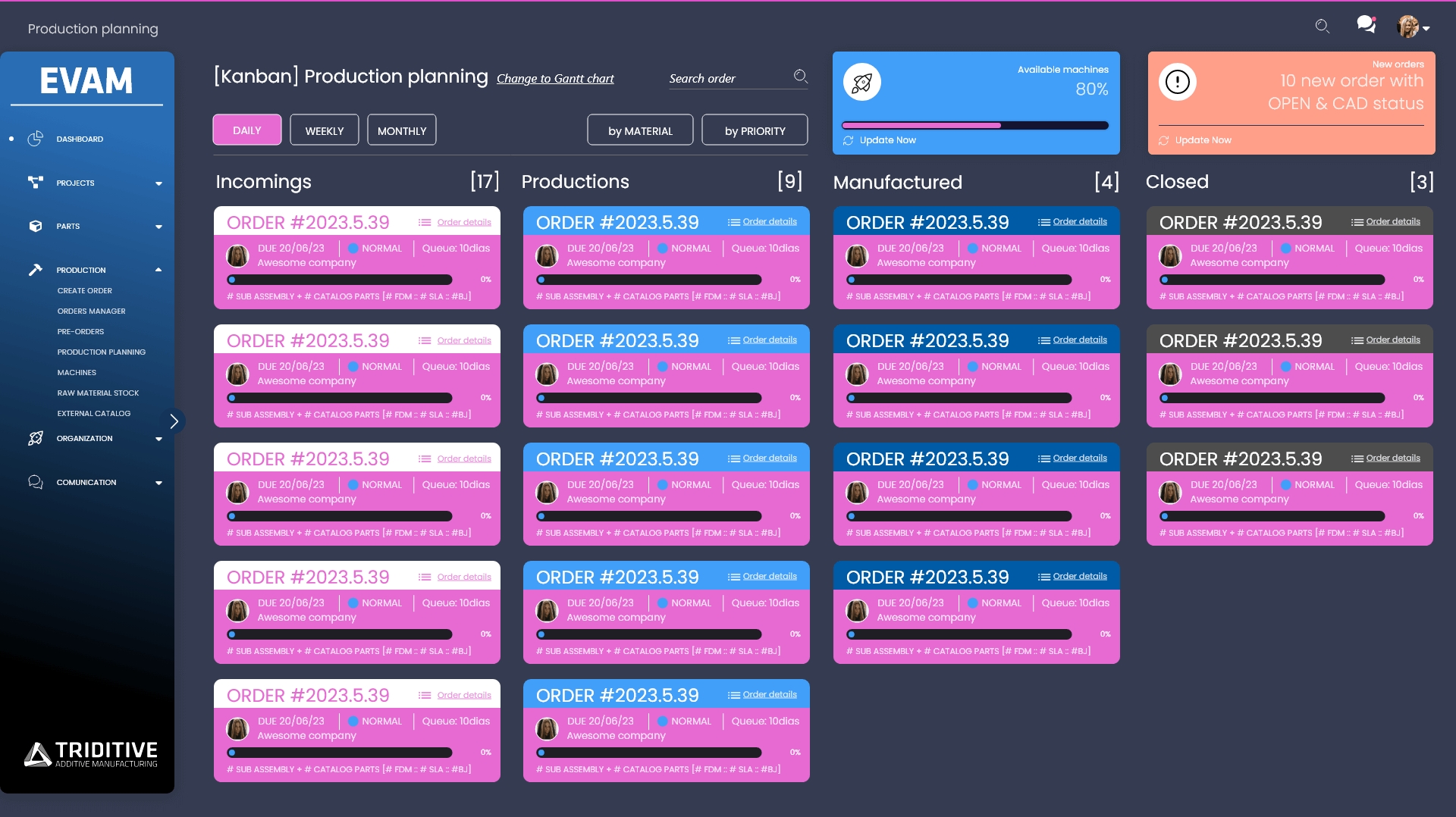
The production manager has at its disposal several tools to plan the production in an easy and efficient way, being able to visualize the information by status, grouping by material or Buils.
By means of the Kamban or Gantt you can modify the order of execution of the orders.
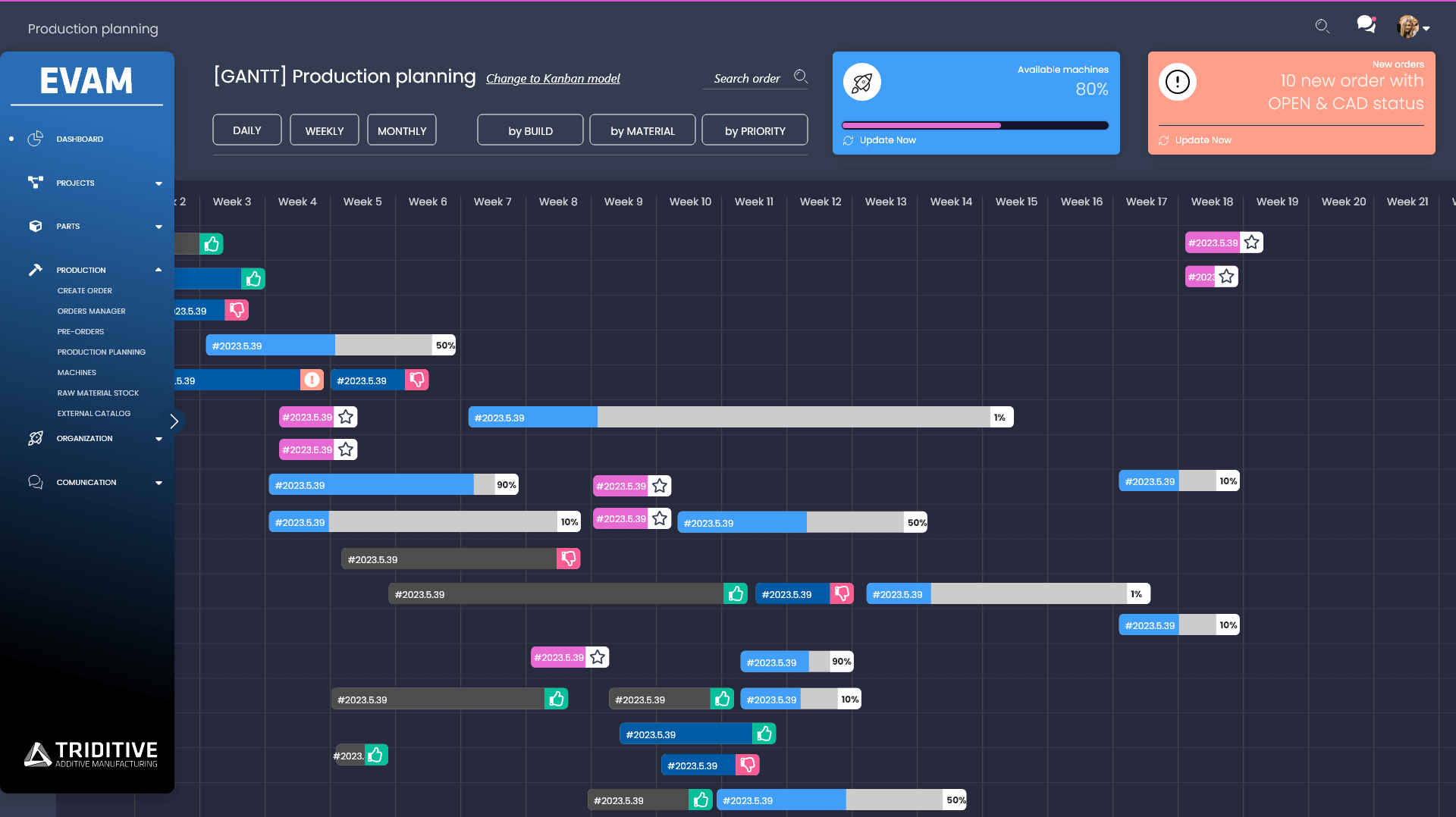
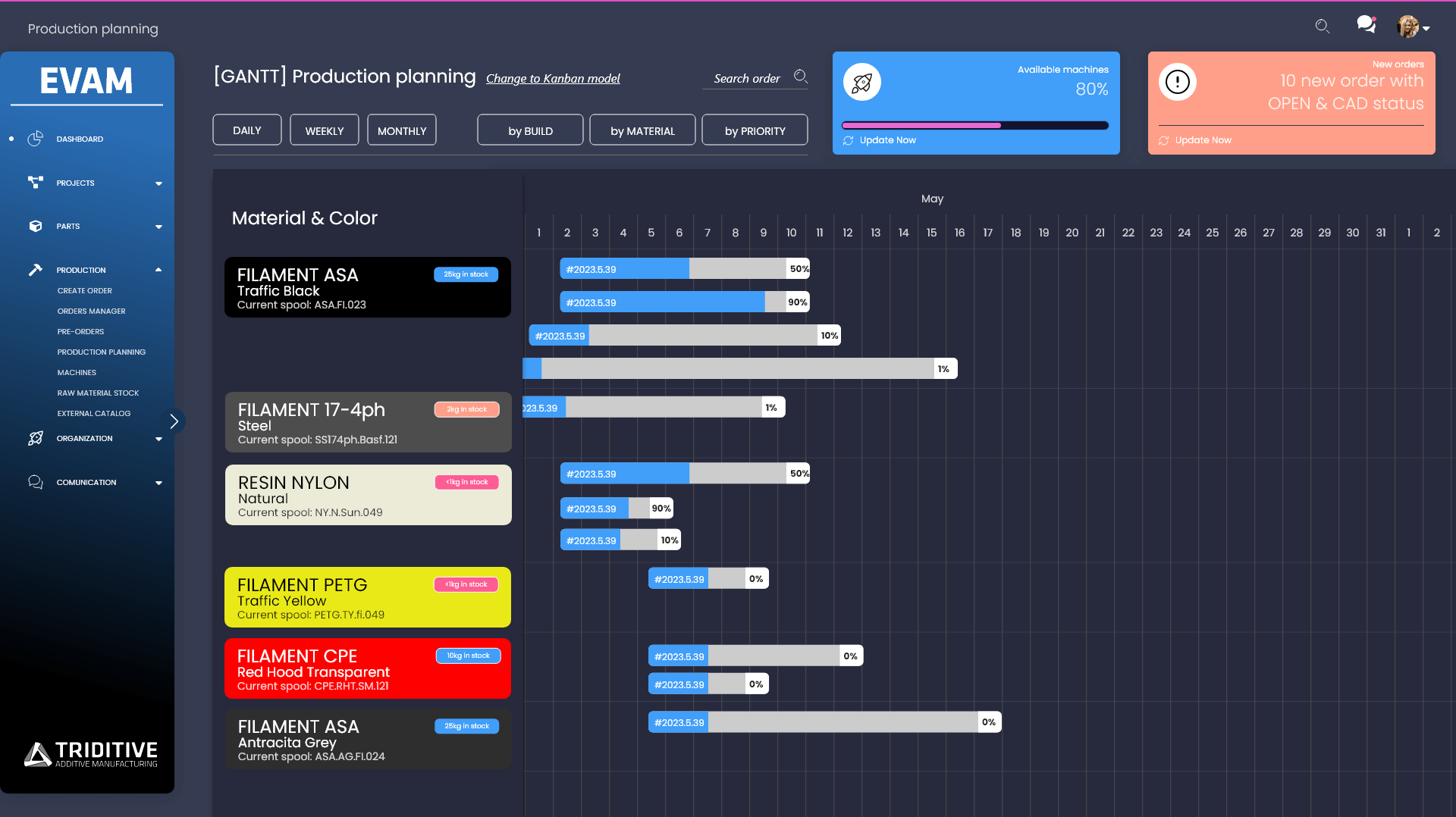
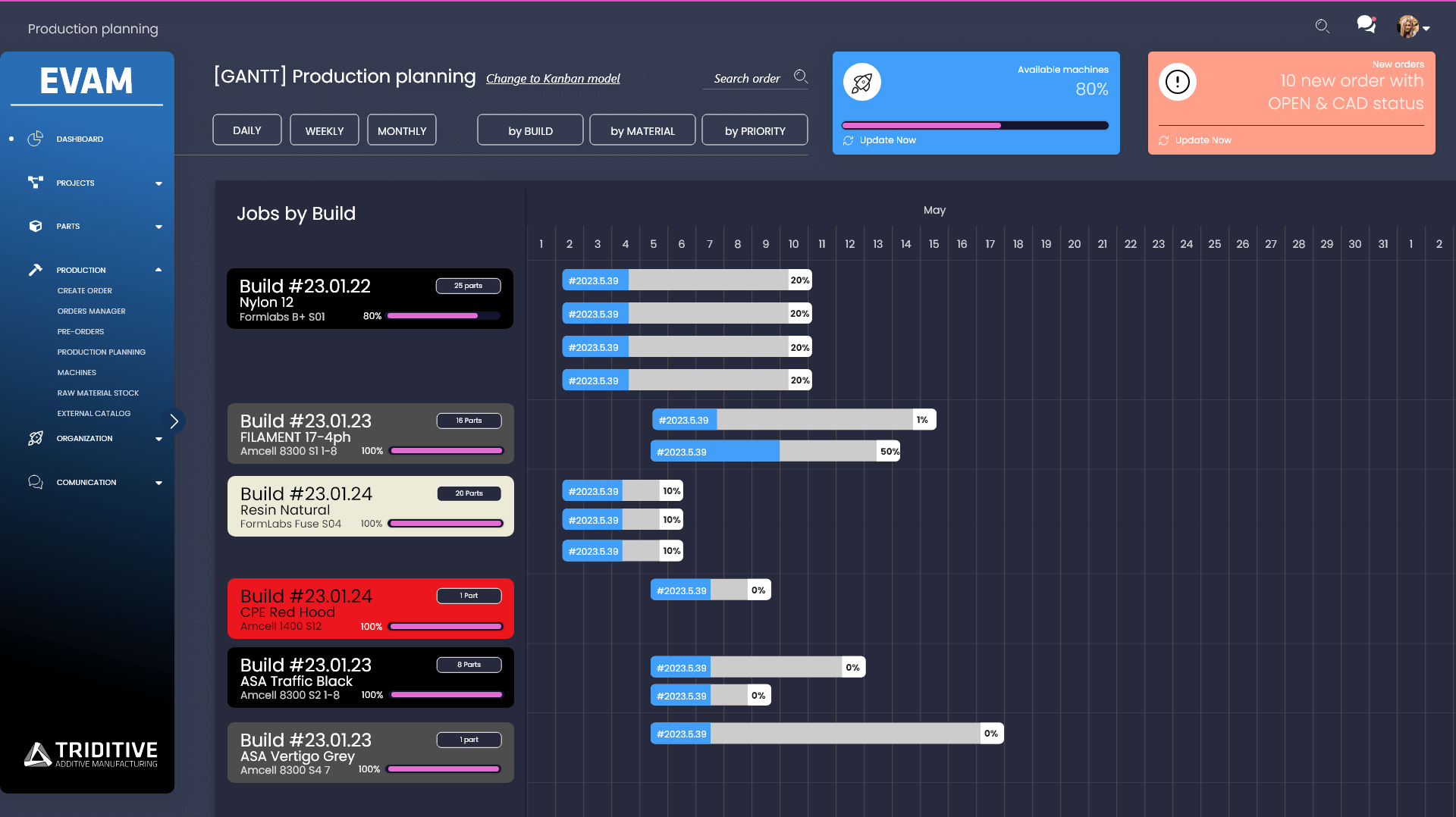