Mass production Cost-Effective in metal and polymers
Amcell 8300®
AMCELL 8300 is an automated additive manufacturing cell for the mass production of high complexity and precise final parts, controlled by EVAM Software to manage production orders, in-process control, and reduce machine downtimes.
Manufacturing orders, process monitoring, feedstock control, smart environmental control, are just some of the features that make AMCELL 8300® a real platform for mass production.
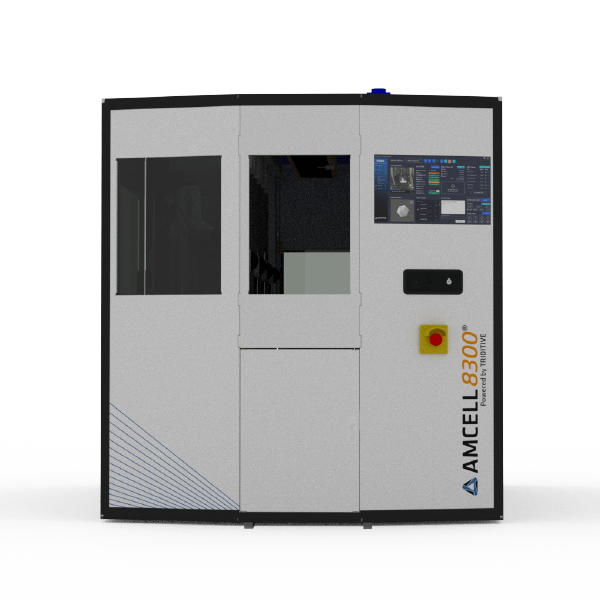
Accurate and functional parts with AMCELL®
- Polymers
- Composites
- Metals
- High tolerance
- Mass production
EVAM Software
- Centralized control and monitoring
- Feedstock smart control
- Production optimization
- Printer integration
- Build simulation
- Scheduling
- Shopfloor connectivity
- Quality and process monitoring
- Traceability
- Mass production
Interested in AMCELL 8300®?
AMCELL 8300 is designed and manufactured by Triditive. Automated Additive Manufacturing is one of those changes with the potential to transform everything. A technology that allows to scale the production exponentially.
Intelligent Automatic System
Enables 24/7 functional final parts production.
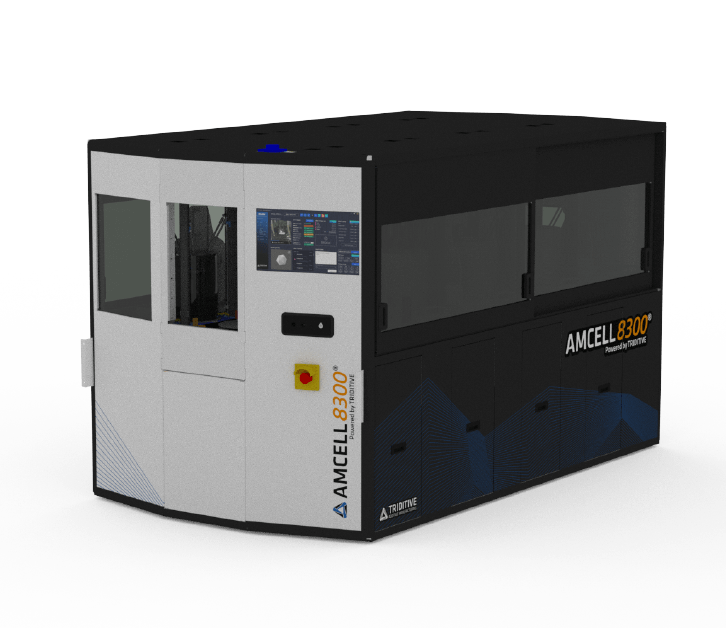
Software-controlled workflow and process monitoring
AMCELL 8300® includes EVAM Software®, the most advanced production control and remote monitoring solution
Automatic calibration
Each printhead is automatically calibrated before each printing job to ensure the highest quality of the final part.
Automatic 3D Printing parts
The printed part is ejected to the automatic storage module and a new platform is loaded to ensure 24/7 production.
Automatic storage
Traceability and automatic storage of printed parts.
AMCELL 8300 + TRACED
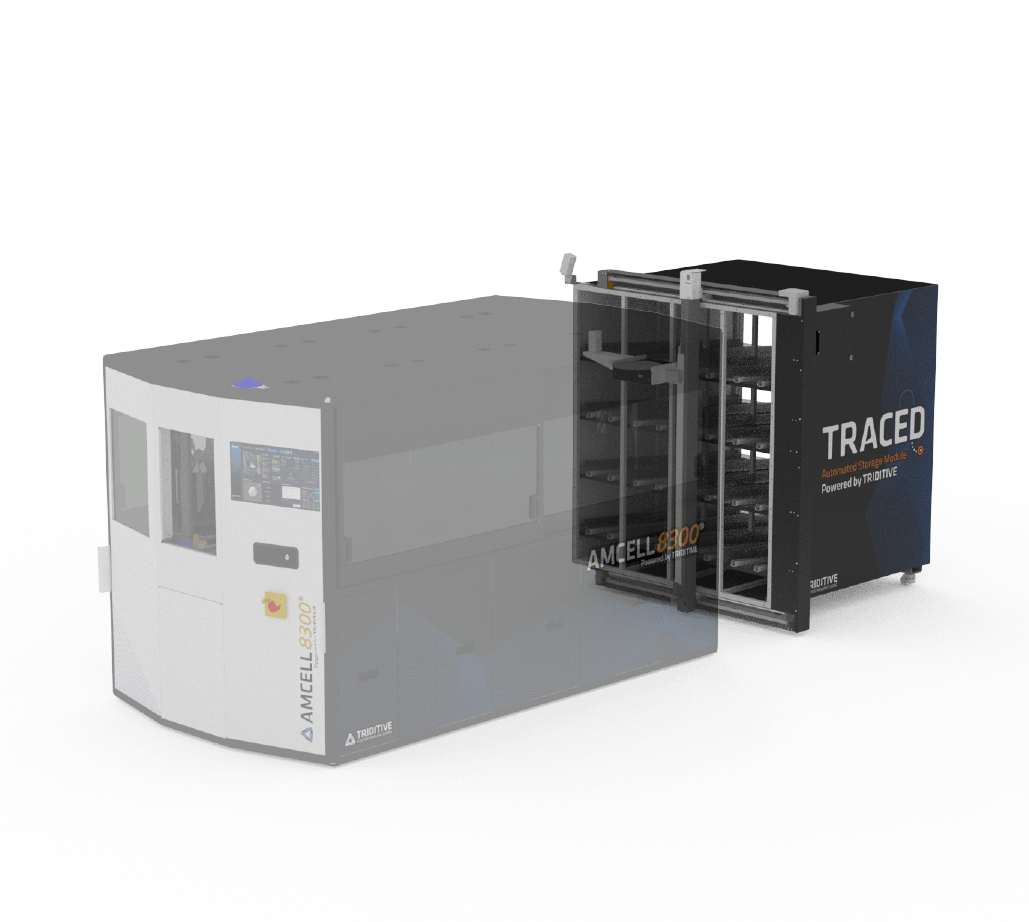
Our Materials
We print in a wide range of materials for your convenience.
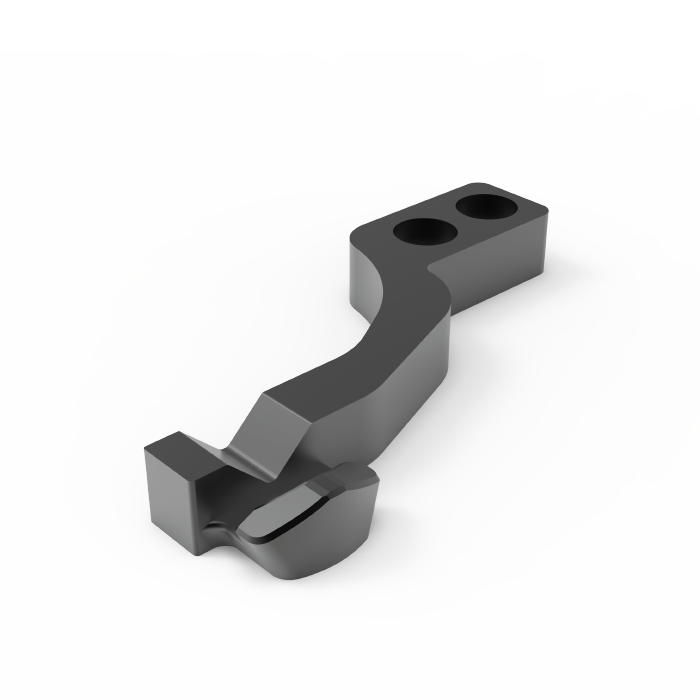
Metals
The advantages of metal 3D printing are that it has the potential to be more cost-effective, especially at low volumes, for parts that are difficult to machine due to their complexity or material.
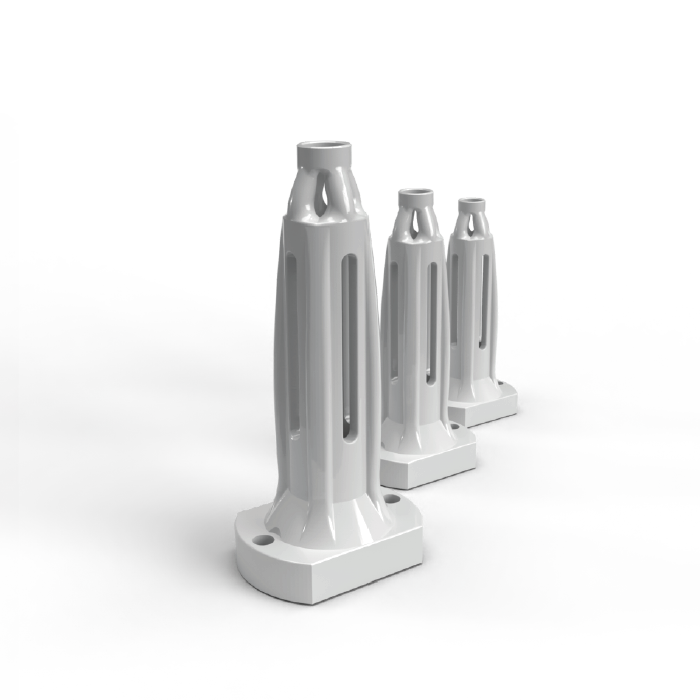
Polymers
We can produce functional and complex polymer parts with the strength, dimensional accuracy and finish quality needed for high-volume production.
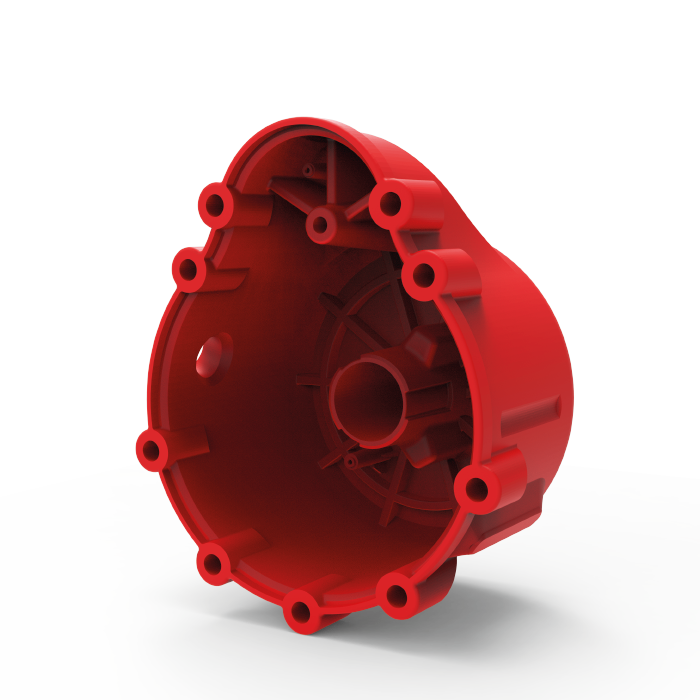
Composites
Composite materials are typically used to improve the strength, stiffness, heat resistance, and durability of traditional 3D printable parts.
AMD Technology in Metals
Automated Multimaterial Deposition® (AMD) is an additive manufacturing process. The main innovation that incorporates our technology is automation and its capability to manufacture parts in polymers, composites, and metals, even at the same time.
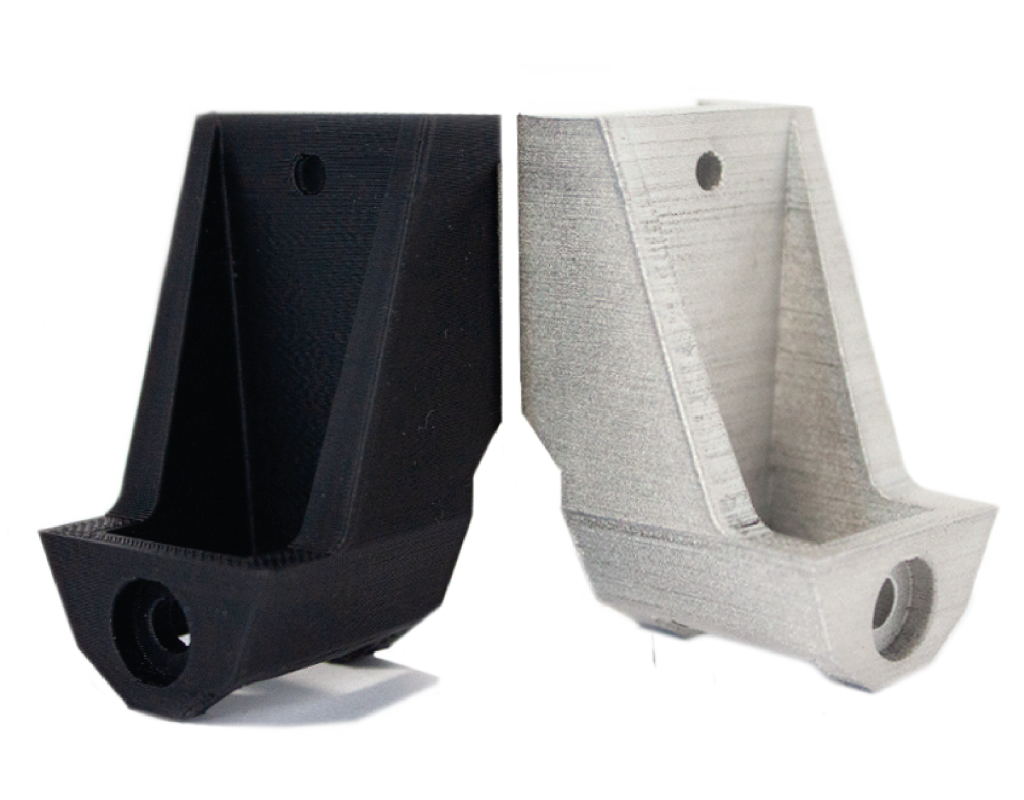
Technical Specifications
Technical Information
- Build rate: 2 Tons polymer/year - 8 Tons metal/year
- Maximum printing height: 300mm
- Maximum printing area: 260mm
- Extruder system: Direct (+ secondary extruder). Filament sensor integrated
- Nozzle diameter: 0.4 - 1.2 mm
- Minimum layer height: 50 μm
- Number of robots: 8
- Build chamber: Heated with temperature control, Bofa® filtering system
- Build chamber temperature: 60 ªC IR Heating System
- Material Storage: modular up to 12kg spools with humidty control
- Monitoring: IP Camera
- Pneumatic system: Integrated
- External dimensions: 3,4 x 2 x 2 m.
- Unloaded weight: 1300kg.
- Automated security lock: Integrated
Manufacturing Platforms
- Platform feeding system: Automatic
- Ejection system: PTS Platform Transfer System
- Build platform: Heated up to 150 ªC
- Build platform material: Vitroceramic glass (customizable)
- Build platform calibration: Automatic
- Final parts storage: Automatic TRACED
Manufacturing Materials
Polymers: ABS, ASA, CPE, HIPS, IGLIDUR I150-PF. PA,PC, PETG, PLA, TPU, VYNIL.
Composites: PA+ARAMIDE, PA+CF, PC+ABS, PC+PBT
Metals: SS316L, SS17-4PH, INCONEL, TITANIUM.
Interested in AMCELL 8300®?
AMCELL 8300 is designed and manufactured by Triditive. Automated Additive Manufacturing is one of those changes with the potential to transform everything. A technology that allows to scale the production exponentially.